リニューアブル
日本山村硝子株式会社・
株式会社山村製壜所
「Momi Glass」で挑む
ガラスびんの3R+
リニューアブルと
サーキュラーエコノミー
「3R+Renewable」としてのMomi Glassは、日本国内のもみ殻産廃をガラスびんの水平リサイクルにアップサイクルすることで産廃が資源となり、ガラスびんとして生き続けることができるガラスである。
お米の「もみ殻」をガラスびんの主原料である"けい砂(シリカ)"の代替として使用したガラスびん「Momi Glass」が、日本山村硝子株式会社とグループ会社である株式会社山村製壜所の共同で技術開発・工業化されました。今までのガラスびんは3Rが完全に成り立つ容器として認知されてきましたが、Renewableという新たなガラスの可能性を実現したものです。ガラスびんの原料に再生可能なバイオマス(*1)を使うことで、より環境負荷が低く、持続可能なガラスびんの技術開発と工業化の事例を紹介します。
*1 バイオマス:動植物などから生まれた資源の総称。再生可能な、生物由来の有機性資源で化石資源を除いたもの。
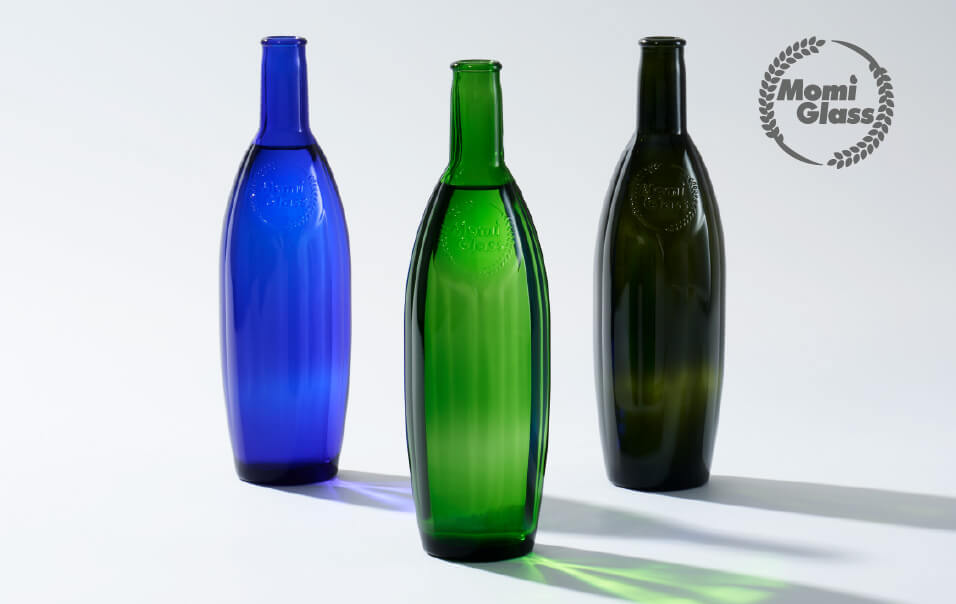
総合ガラスびんメーカーとしての理念
一人ひとりの暮らしを豊かに未来の環境を心地よく。
サステナブルな未来に貢献する、ものづくり企業であり続ける
日本山村硝子株式会社は1914年に創業し、ガラスびんを中心として事業を展開して今年110年を迎えました。1973年には家庭ごみから資源ごみとしてガラスびんを分別回収して「びん to びん」リサイクルする日本初の分別回収を行政とともに開始し、来るべき循環型社会に備えた仕組み作りを行ってきました。現在は、4つのセグメント(ガラスびん、プラスチック、ニューガラス、エンジニアリング)のカンパニー制と独立したCSR推進室と環境室、これらを統括するコーポレート本部で事業を展開・運営しています。
グループ会社である株式会社山村製壜所は1984年に日本山村硝子株式会社の100%子会社として設立し、大量生産とは異なる多品種・少量生産に特化し、多彩な表現力と技術で小ロット、自由な形、多彩な色の個性豊かな高品質のガラスびんを提供しています。
山村グループは、人々のより快適な暮らしと地球環境の未来のために、グループ経営ビジョンを「100年先も必要とされる会社」と定め、永きにわたり受け継がれてきた人と環境への想いに重点を置きながら、サステナブルな未来に貢献する社会から必要とされる企業グループであり続けるため、一丸となって持続可能な未来づくりに挑み続けます。
開発コンセプトの探索と技術開発
将来の課題解決のため、
サーキュラーエコノミーからのアプローチ
日本山村硝子株式会社の環境室の業務は、環境マネージメントと環境技術開発です。環境技術開発のコンセプトを探索するに当たっては、サーキュラーエコノミーの観点からガラスびんのリサイクルに止まらないガラスびんと循環経済の連関や将来の課題解決への貢献を意識しました。
今回のコンセプトは環境をキーワードにした新しいガラス素材の開発とし、廃棄資源やカーボンニュートラルとなる資源から、ガラスびんの原料であるけい砂・石灰石・ソーダ灰に代替できる原料を探索しました。
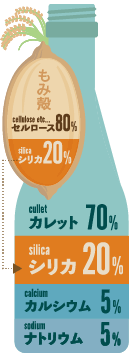
2020年に開発スタッフから「もみ殻」でガラスをつくりたいとの提案がありました。当初は「もみ殻」という有機物をガラス原料に使用することに戸惑いがありましたが、「もみ殻」にはガラスびん原料のけい砂の主成分であるシリカが約20%含まれていることから、ガラス原料に使用できる可能性が想定できました。「もみ殻」は年間200万トン以上も廃棄されていることがわかり、未利用の「もみ殻」をガラス原料に使用することでガラスびんのマテリアルフロー外の廃棄物をガラス原料にアップサイクルできるので、「再生可能資源」と「枯渇性資源」が循環する仕組みを構築することを目指すサーキュラーエコノミーに合致します。また、「枯渇性資源」を原料としてきたガラスびんが「再生可能資源」を原料化することで、ガラスびんでも「3R+Renewable」が実現できることも大きな意味があります。
さらに、「もみ殻」は植物由来のバイオマスですので、成長過程で光合成によりCO2を吸収しているため、「もみ殻シリカ」の焼成工程で発生するCO2はオフセット(*2)できます。
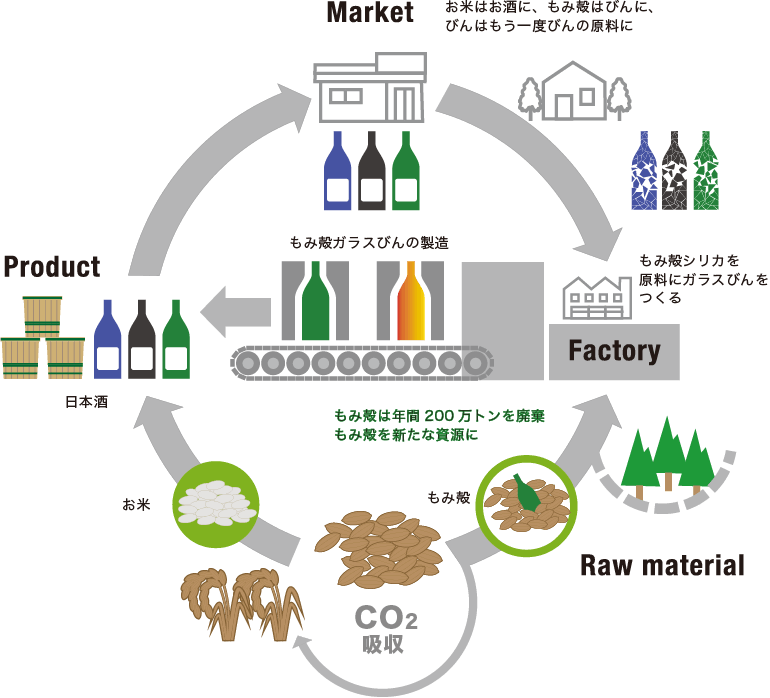
実験でけい砂を「もみ殻由来シリカ」(以下、「もみ殻シリカ」)に100%置き換えてガラスサンプルを作製し、原料やガラスサンプルの物性等のデータを取り、評価と課題を抽出しました。その結果、「もみ殻シリカ」100%使用してのガラス化は可能ですが、原料とするためには条件があることが判明しました。
その条件は炭素含有量でした。「もみ殻シリカ」にするには「もみ殻」を焼成して有機成分を焼き飛ばしますが、一次焼成だけでは不十分であり、二次焼成することで使用可能な原料となり、原料調合比率で組成調整が可能となりました。
*2 (カーボン) オフセット:自らが排出したCO2などの温室効果ガスを他の場所での排出削減や吸収に貢献することを通じて相殺すること。
もみ殻シリカを100%用いたガラスの実験プロセス
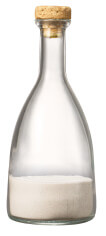
けい砂
もみ殻の
セルロース等を
熱処理除去
一次もみ殻シリカ
さらに熱処理を
行い
シリカ90%
以上に
二次もみ殻シリカ
もみ殻由来原料でガラス製作
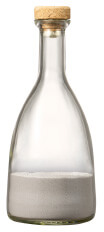
もみ殻シリカ
- 通常の
無色ガラス -
けい砂
- 実験1
-
けい砂
→↓一次もみ殻シリカ
- 実験2
-
けい砂
→↓二次もみ殻シリカ
炭素を除去し透明のガラスとなる。一方、鉄分の含有により若干緑色に着色。
「もみ殻シリカ」使用のガラスびんの工業化
「社会貢献」を優先、
工場製造レベルでの諸問題も現場の裁量で解決
実験による検証をくり返しながら、技術開発の目途がつき、工業化したいと考えていた2021年、山村製壜所の社長との会話の中で、「もみ殻シリカ」を使用したガラスの技術開発が話題となり、興味を持ってもらいました。
当時、山村製壜所では今後の事業戦略を検討していたタイミングでもあり、工業化・商品化に共同で取り組むこととなりました。
商品化に当たっては利益優先ではなく社会貢献を優先することとし、工業化への取り組みを開始しましたが、ラボレベルでは可能なことも、ファクトリーレベルでは簡単には行かないことを痛感しました。問題は「もみ殻シリカ」の嵩密度(*3)でした。「もみ殻シリカ」はけい砂に比べて嵩密度が非常に小さく、同じ質量でも約7倍の容積となるため、工場製造時に既存の設備ではオーバーフローするため改善が必要となりました。
最初の問題は調合時に使用するもみ殻シリカの原料受け入れホッパーへの投入でした。「もみ殻シリカ」の納品は底開きタイプではないフレコンバッグのため、ホッパーに直接投入できず、フレコンバッグからショベルでホッパーへ手投入するのが大変でしたが、電動ウィンチを延長し吊り上げてそのままホッパーのほうに持って行けるように改造して解決しました。さらに、原料補充用ホッパーはけい砂の使用を前提としているため、けい砂に比べ嵩高い「もみ殻シリカ」では容量が足らず、嵩増ししたホッパーにも改造しました。これらの改造により効率が上がり、1日分の「もみ殻シリカ」を継続して調合できる受け入れ設備になりました。同様に、「もみ殻シリカ」の計量装置投入も課題となりました。「もみ殻シリカ」は比重が小さく、フワフワしたものなのでスムーズに原料が落ちない現象も起こりました。原料が減るごとにホッパーを叩いて落としていましたが、手間がかかるのでエアの力でタイミングよく叩くよう設備改造してクリアしました。
これらの問題解決では臨機応変な設備改造を現場の裁量で実行できたことが大きいと思います。びんの試作は合計で6回テストし、検査も問題ないところまで辿り着きましたが、工場の製造ラインで連続してトン単位の製造をすることはやはり大変でした。現在は、「もみ殻シリカ」の納入からリアルタイムにいつでも製造できるライン設備が完成し、工業化できています。
*3 嵩密度:粉体の質量をその占める嵩体積で割った値。単位嵩体積当たりの粉体重量のこと。
製造工程
-
底開き出来ないフレコンバッグを、固定チェーンブロックを延長、電動化して投入口まで移動できるようにした
-
限られた副原料タンクを工夫して使用
-
嵩高いもみ殻原料に対応する嵩増しホッパー
-
軽くふわふわしたもみ殻原料、計量時に調合遅れとならないようプログラムを工夫
-
軽くふわふわしたもみ殻原料、混合後に再分離、飛散しないよう、水分影響が出ない範囲で散水して搬送
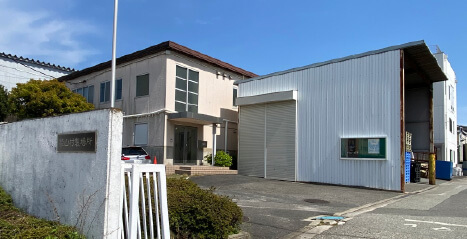
山村製壜所の外観
「Momi Glass」の展開と未来
社会貢献価値の共通理解で社会実装、
サーキュラーエコノミーの実現を目指して
「もみ殻シリカ」を原料に使用したガラスびんを「Momi Glass」(容量720ml)と名付け、商標登録もしました。コンセプトボトルは「もみ殻」をイメージしたフォルムとし、中央のエンブレムは稲穂をモチーフにしました。
このコンセプトボトルの原料構成は、70%がカレット、残り30%のうち20%がけい砂、10%がソーダ灰と石灰石です。使用するけい砂の5%を「もみ殻シリカ」に代替しています。このガラスびん1本に使われる「もみ殻」の量は720mlの日本酒の醸造に使用される酒造米の約50%に相当します。このことは「Momi Glass」に入った日本酒は、使用した酒造米の約半分の「もみ殻」をガラスびん主原料にアップサイクルし、その後は「ガラスびん」として何度も水平リサイクルされることになります。
「Momi Glass」は社会貢献と位置付けていますので、高収益を上げることを想定していません。しかしながら、「もみ殻シリカ」はけい砂よりも調達コストが大幅に高く、通常のガラスびんよりも高コストとなるため、販売価格も高くせざるを得ません。
「Momi Glass」をご採用いただき社会実装するには、コストだけではない社会貢献やブランドの付加価値の共通理解が不可欠と考えています。つまり、「Momi Glass」製品を使うことは環境貢献するということです。このため、「Momi Glass」をお客様にご案内する際には、「3R+Renewable」による資源循環、サステナブルな未来、サーキュラーエコノミーの実現などへの貢献ができることを説明しています。
当社関西本社と山村製壜所のある兵庫県には清酒と酒造好適米の名産地があります。また、原料製造所とカレット(再生原料)事業者も兵庫県内にあるため、県内の清酒メーカーに「Momi Glass」を採用していただけると、さらに「地産地消」の促進や「地域循環共生圏」の構築にも貢献できます。
「Momi Glass」のその先へ
ガラスびんのサーキュラーエコノミーの深化を目指して、
社会貢献価値の共通理解で社会実装
日本山村硝子株式会社の創業家である山村徳太郎は、すでに1973年に将来の循環型社会を想定し、空きびんを資源ごみとして扱う活動を開始しています。その後、1975年には日本初の分別回収をガラスびんで実現、全国展開し、容器初の水平リサイクル「びん to びん」の仕組みを構築、発展させました。このように、当社には資源循環のDNAがあり、今回の「Momi Glass」の開発もこのDNAによるものといえます。
ガラスびんメーカーとして「びん to びん」の水平リサイクルを継続することはもちろんですが、ガラスびんの代替原料となる未利用資源の探索と原料開発を進め、「再生可能資源」を使用したガラスびん製造でサーキュラーエコノミーを実現し、枯渇性資源消費量とCO2排出量の削減に極限まで挑戦していきます。
Momi Glass開発プロジェクトの皆さん
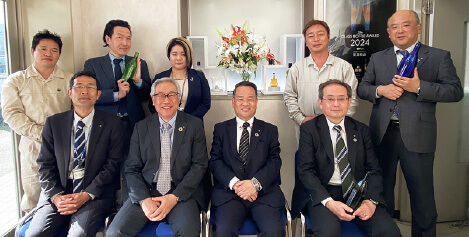
- 後列左側から
- 製造部/島谷さん 環境室/山本さん 環境室/堀さん 製造部 課長/細川さん 営業部 課長/橋本さん
- 前列左側から
- 環境室室長/辻さん 執行役員環境室管掌/植田さん 代表取締役社長/浅野さん 取締役 営業部部長/中野さん
青色=日本山村硝子 緑色=山村製壜所
もみ殻+ガラスびん

ガラスびんのシリカ(珪砂)原料のうち5%をもみ殻原料に代替したガラスびん製品は、清酒製造時に発生する廃棄もみ殻の約50%を有効利用できます。本技術によるガラスびん入りの日本酒は、「消費者が日本酒を飲むことで、製造時の廃棄物削減に貢献できる」という、消費者と生産者が共同でサーキュラーエコノミーを実現する世界初(当社調べ)の試みになる画期的な製品です。
なお、もみ殻を使用したガラスは1500℃程度の高温でガラスびんへと成型されるため、お米由来のアレルゲンがガラスに残存することはありません。また、従来同様のガラスびん製造手法を用いるため、従来製品の品質と変わりません。
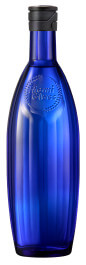
ダークベネチアンブルー瑠璃
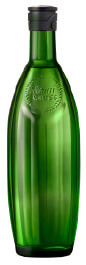
エメラルドグリーン青緑
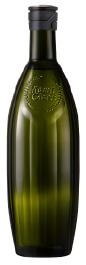
ブラックグリーン深緑
ボトルのデザインは、もみ殻イメージを具現化しています。
また、Momi Glassロゴをあしらった彫刻が、個性的なアクセントになっています。
本件に関するお問い合わせ先
日本山村硝子株式会社 環境室
TEL:06-4300-6060
URL:https://www.yamamura.co.jp/
E-mail:nyg.eao.tec@yamamura.co.jp
株式会社山村製壜所 営業部
TEL:0798-43-1301
URL:https://www.yamamuraseibin.jp/
E-mail:yb-contact@yamamura.co.jp